The production process of woodworking saw blade UKO Blog
There are commonly used carbon tool steel (T9, T10) and high-speed steel for woodworking saw blade body. Tungsten cobalt (Gy) and tungsten titanium (YT) are commonly used for carbide blade. Tungsten cobalt cemented carbide with high hardness and strong impact resistance is widely used in woodworking saw blades.
Carbide saw blade of the same size has a different number of teeth. The more teeth there are, the smoother the cutting surface is, but the friction force is large and the processing sound is loud. There will be many openings and circular holes on the saw blade. When the saw blade is cutting materials at high speed, a lot of heat will be generated. The metal will expand and contract when it is hot. By increasing the opening, the saw blade can freely expand and expand at high temperatures, which can avoid the deformation of the saw blade.
Weld carbide teeth.
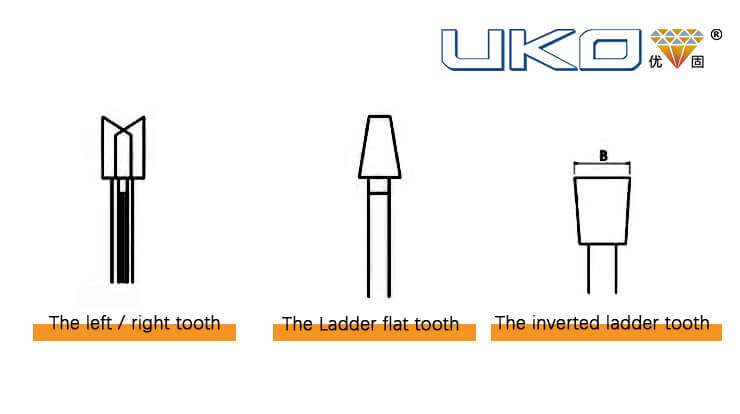
The left and right teeth are widely used with high cutting speed, sharp teeth, and good cutting quality. Suitable for cutting, hard solid wood, density board, multilayer board.
Ladder flat tooth is a combination of trapezoidal tooth and flat tooth. It can reduce the phenomenon of tooth collapse when cutting. It is suitable for cutting a wood-based panel and fireproof board.
The inverted ladder tooth is suitable for the slotting of thick wood plate, and then the cutting process is completed by the main saw. The blade is too thick to cut.
The saw tooth is made of cemented carbide, which has a high heat resistance and wears resistance, and the service life of the saw blade is greatly prolonged. The saw teeth and cemented carbide are heated to 700 degrees and welded together with flux (special copper powder). After welding, it will be tempered in 100 degree oven to improve durability and wear resistance.
Then you can start grinding teeth. If the welded alloy cutter head has no cutting edge, grind the front, back and side of the saw tooth according to the angle of the sawtooth to make it sharp.
Laser engraving, laser printing the required font, and trademark on each saw blade.
Inspection: check the flatness of the saw blade body after heat treatment with a level gauge, check whether the cemented carbide welding is firm with projection, and check the size of the central hole of the saw blade with a plug gauge.